Getting the Most from Pre-Engineered Buildings
Pre-engineered metal buildings (PEMBs) offer a compelling path for certain project types, particularly large-volume athletic facilities, when deployed thoughtfully. At ARC, we’ve used PEMB systems in a variety of contexts, with varying degrees of success. Our experience has highlighted not just the efficiencies of these systems, but also their limits, and the importance of careful planning.
The Upside of PEMB Systems
The appeal of PEMBs is clear: speed of erection, potential cost savings, and systemized building envelope components like insulated metal panels that simplify code compliance. But those benefits are best realized when the building design leans into the strengths of the system. Simple box forms on flat sites, like at Bentley Arena, for example, allow the PEMB supplier’s standard systems to shine. Complicated sites or hybrid building programs can create coordination challenges that impact both cost and schedule.
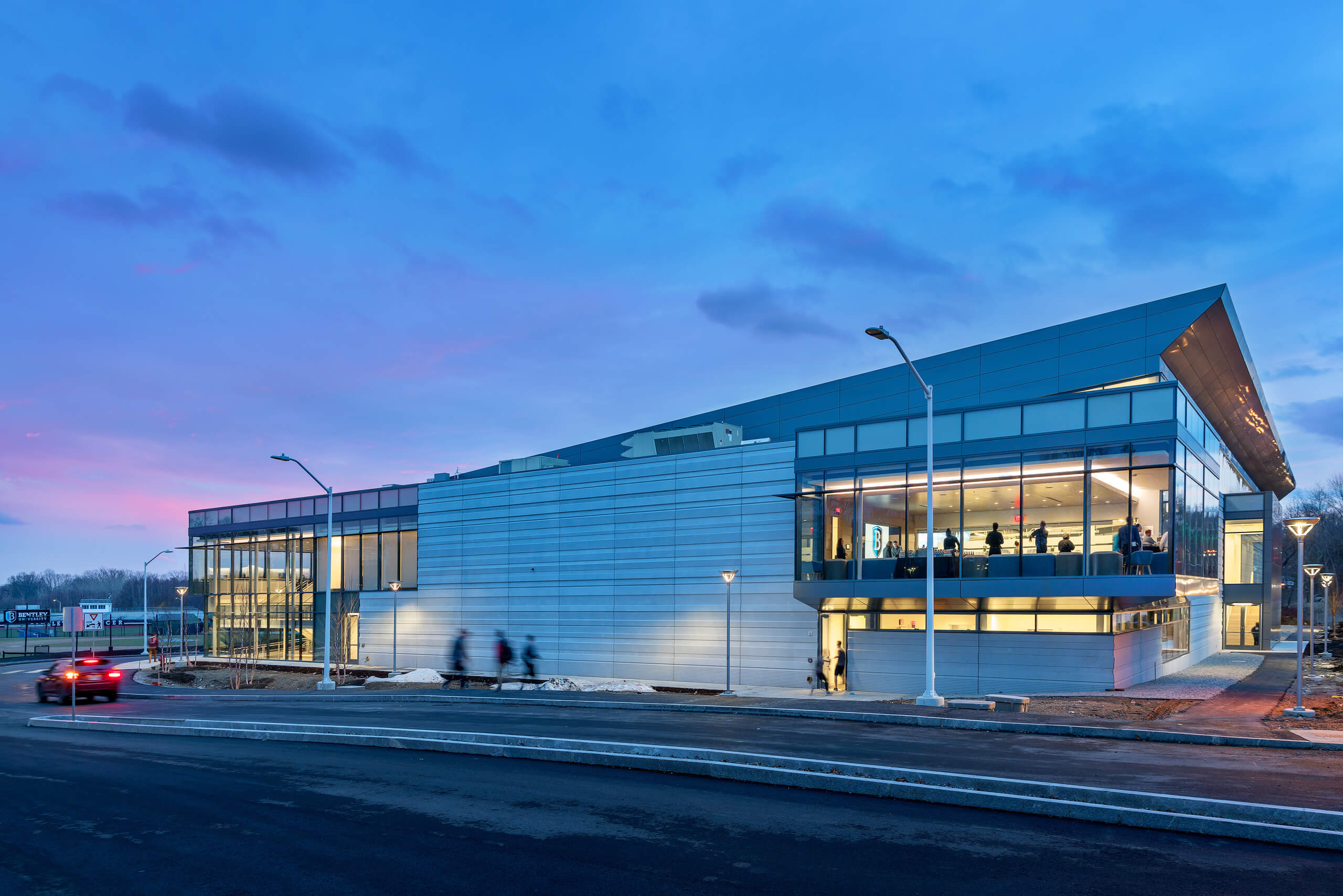
Challenges in More Complex Conditions
The experience at GCDS highlighted the limits of the PEMB approach on a more demanding site. A steep slope across the site and a garden level under one-third of the building, meant the steel framing had to navigate significant elevation changes and integrate with retaining and foundation elements. While the PEMB structure itself functioned well for the court volume, coordinating it into the broader building geometry proved complex and required more customization than originally intended, undermining the efficiency typically associated with PEMBs.
This project also reinforced the importance of having the right partners. A construction manager who understands the intricacies of PEMB delivery and can shepherd the process through all phases, and a manufacturer’s representative who is willing to collaborate with the design team to realize the vision. As one installer remarked during our work at Hackley, “PEMB is a building that is meant to be seen from afar and not up close.” It’s a reminder that the more a PEMB is asked to do beyond its standard kit of parts, the more likely the outcome will suffer.
To effectively use PEMBs, the project team has to be responsive, flexible, and have shared understanding of both design goals and system constraints.
Key Takeaways for a Successful PEMB Project
- Use PEMBs Strategically
Apply PEMBs where they perform best, simple, flat sites and open-span spaces. Supplement with conventional framing for more complex or fine-tuned areas of the building. Hybrid structures, like those used at Princeton Day School, can provide the best of both worlds. - Don’t Assume One Size Fits All
Complex sites or multilevel conditions may erode the value of a PEMB. When grade changes are significant, conventional steel can be more adaptable and efficient over the life of the project. - Early Engagement is Critical
PEMBs require clear early definition of structural loads such as scoreboards, solar arrays, mechanical units, and athletic equipment. All these elements must be identified and fully coordinated before the PEMB shop drawings are produced, well ahead of the timeline many teams are accustomed to. - Select the Right Team
Success depends on a collaborative relationship between the architect, CM, and PEMB vendor. Choose a CM with PEMB experience who can guide cost and schedule implications and ensure the PEMB supplier includes a representative who will actively work with the design team to align system options with the project vision. - Stay Within the System’s Strengths
Standard panel systems and finishes offer better value and faster procurement. Pushing for atypical colors, added capacity, or envelope customizations can quickly erode both schedule and cost benefits. - A Structural Engineer is Still Essential
Even when the PEMB vendor provides structural elements, the project still requires a licensed structural engineer to design the foundations, coordinate with site and building loads, and validate the PEMB system. - PEMBs Change the Project Rhythm
The design and procurement timeline for PEMBs is different than conventional steel. Coordination happens earlier and moves quickly. Without disciplined communication among all parties, time savings can be lost to rework and confusion. - Schedule Gains May Be Offset by Coordination Delays
While PEMBs erect quickly, they require a level of early-stage coordination that may not align with typical project schedules. If consultants are brought on late or scope is still evolving, those early gains may vanish. - Conventional Steel Offers More Design Flexibility
At Phillips Exeter Academy, the decision to use conventional steel for the William Boyce Thompson Field House stemmed from the need for below-grade parking, complex program adjacencies, and the desire for maximum long-term adaptability. In that case, the flexibility and sequencing advantages of conventional steel outweighed any potential cost savings offered by a PEMB. - Factor in Expansion and Flexibility
PEMBs are less forgiving when it comes to future adaptability. Structural bays, roof capacity, and load paths are often fixed. If expansion or modification is likely down the road, consider whether a conventional steel system might provide better long-term value.
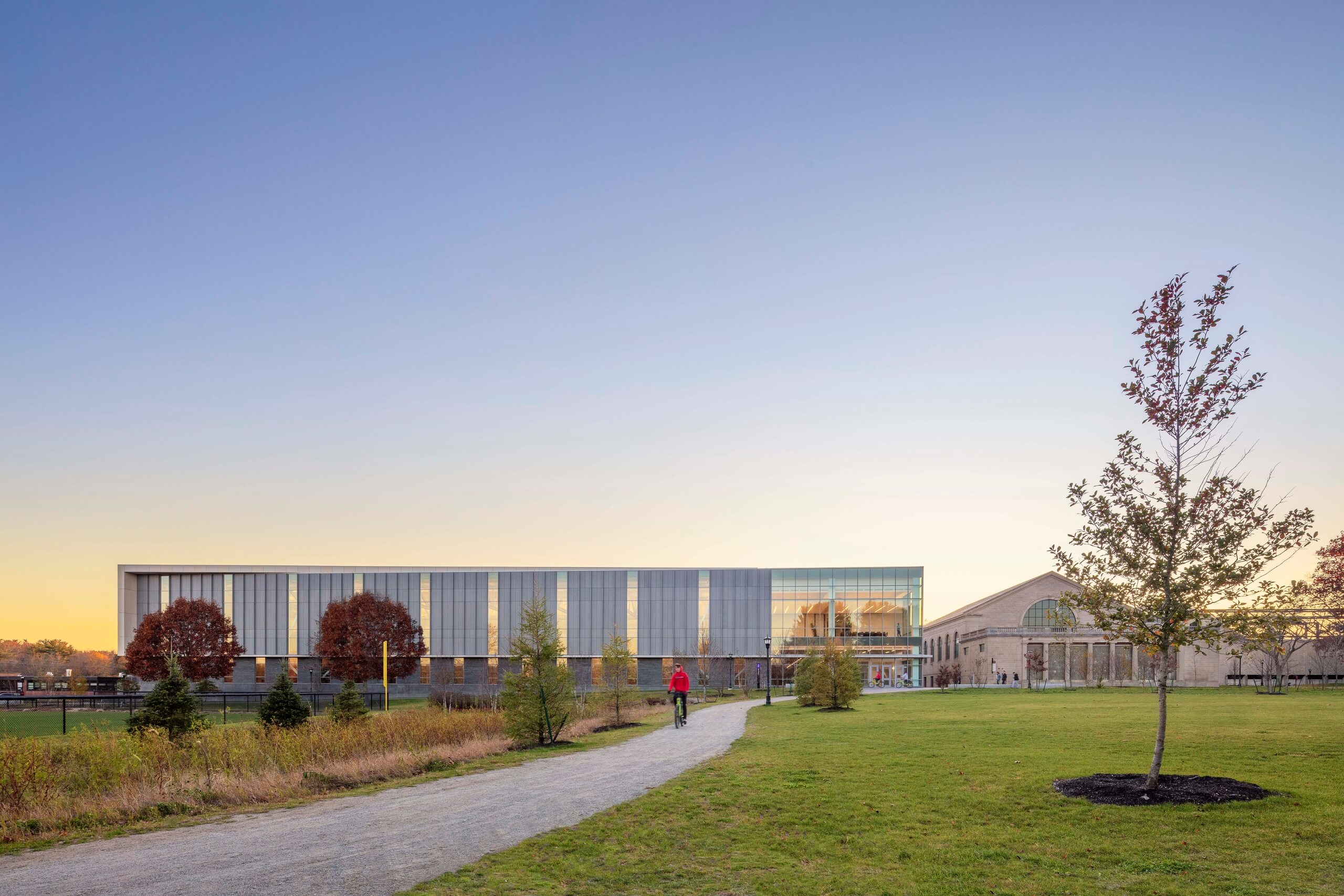
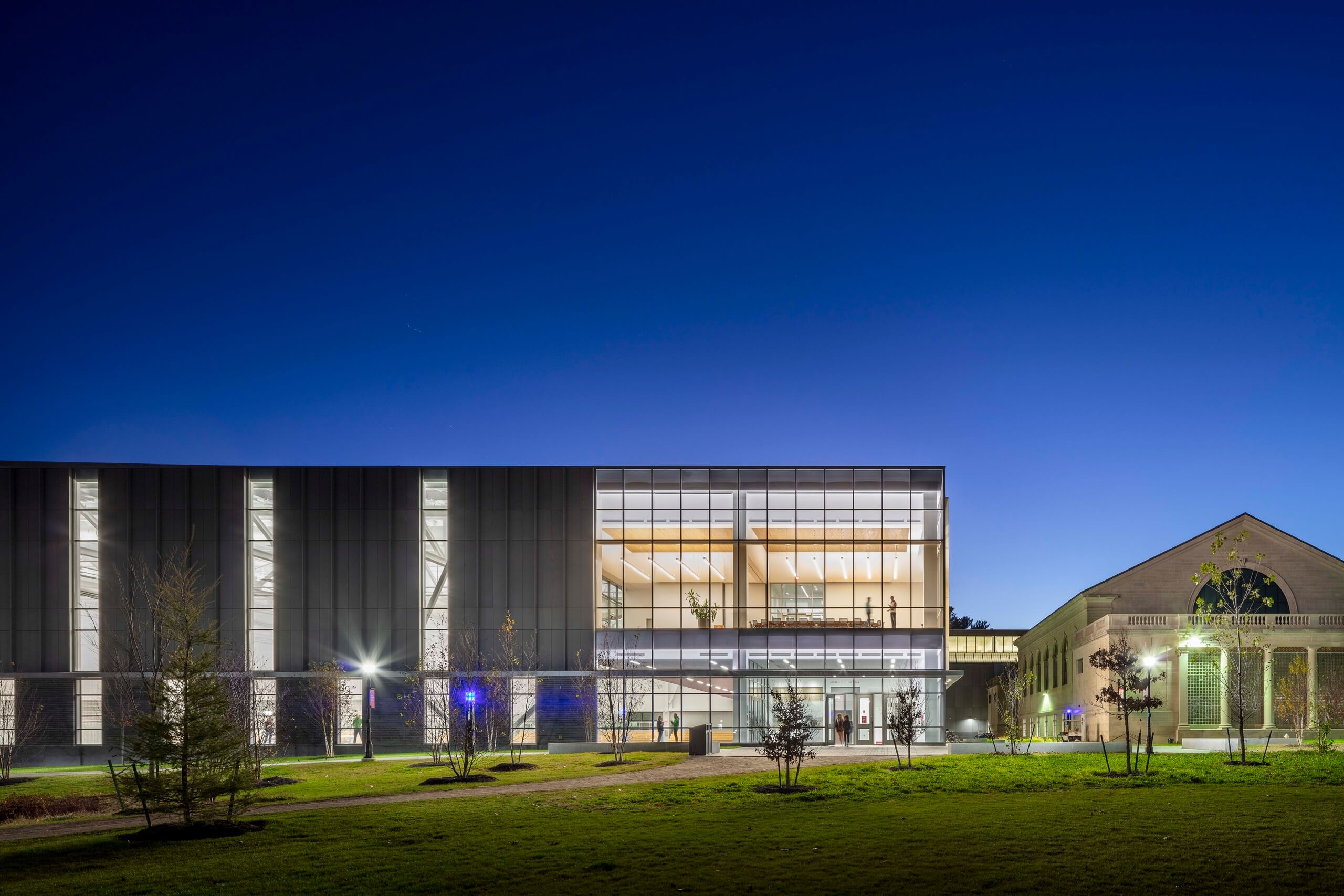
PEMBs are not a shortcut, they’re a specialized tool. When applied in the right conditions and supported by an experienced team, they can deliver real value. But when site constraints or program complexity stretch the system beyond its limits, PEMBs can become more cumbersome than efficient. Success lies in recognizing the difference.